High cost savings through X-ray detection
How X-ray detection enables the shift to recyclable packaging and reduction of waste.
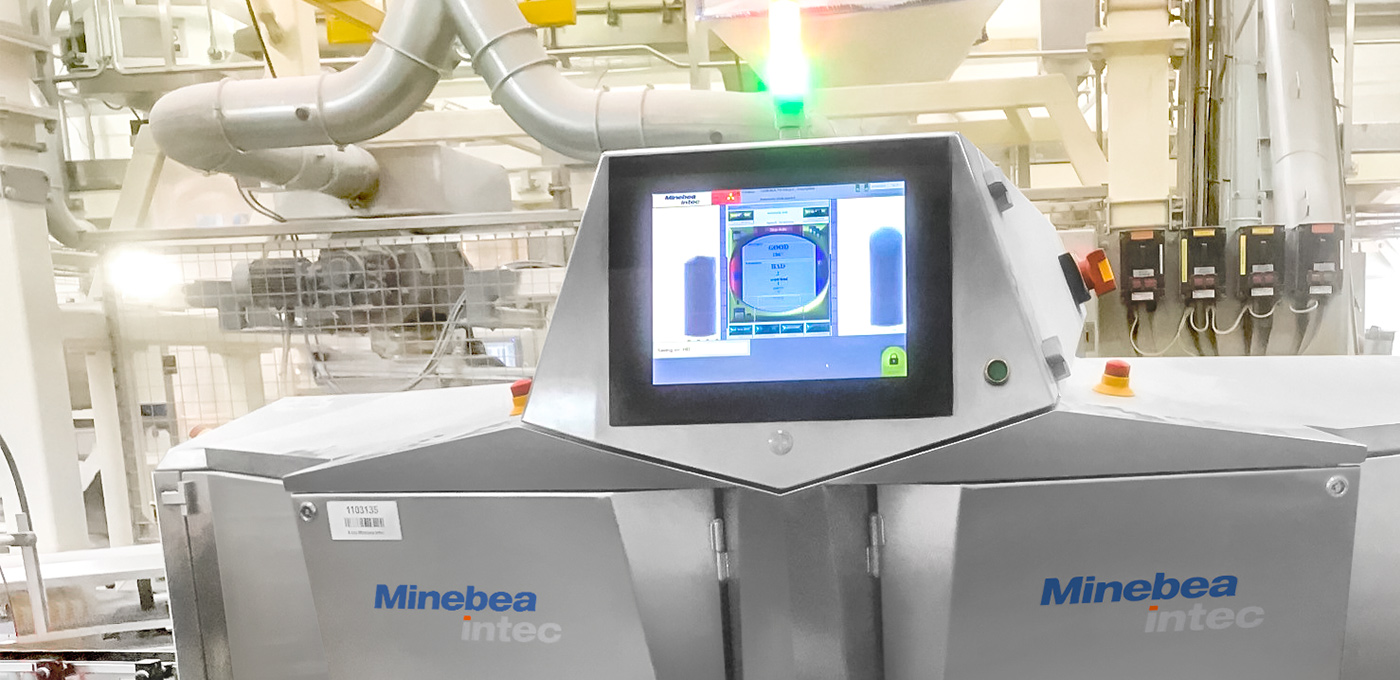
Key facts
Food manufacturers; Premier Foods, Knighton blend, process and pack powdered foods and drinks such as custard, dried skimmed milk and cocoa powder.
Application & Product
Premier Foods, Knighton have moved to end of line testing using the X-Ray inspection system Dymond S to scan complete, packaged products. Prior to this, they were scanning bulk material using metal detection. Testing for ferrous, non-ferrous and stainless steel was done every hour c r eating waste product at a high cost.
Customer benefits
- X-Ray detection at end of line eliminated waste and saved money
- Change of inspection solution greatly reduced cleaning labour and material costs
„Minebea Intec offered the best solution for our needs; the unique design of the Dymond S Side Shoot X-ray system fits perfectly into our production line as it doesn’t take up as much space as other x-rays on the market. The product is saving us £80k each year which is incredible as well enabling us to become more environmentally friendly by reducing waste and using fully recyclable packaging.”
Lee Millward
Engineering Manager Premier Foods, Knighton
Premier Foods, Knighton wanted to transition to packaging that was fully recyclable by replacing a metal lower end with paper. During this process, they also decided to move to end of line testing to try and reduce wastage they were getting from using a Bulk Metal Detector further up the line. The Dymond S has enabled them to achieve both of these objectives and in-turn they’re now making huge annual savings.
By using x-ray they now lose just one container when a reject is detected and can use existing containers with product in to do their routine hourly tests. In addition to metal, other foreign bodies such as glass and stone can also be detected. Lee Millward, Engineering Manager for Premier Foods, Knighton commented “The Dymond S detection range is much better than what we had before, it gives us greater scope to test for smaller foreign bodies.”
The other huge benefit to Premier Foods, Knighton is that it’s saved them time and costs in cleaning, the old reject system had lots of pipework that required cleaning, (especially as it was testing loose powder) whereas because they’re now checking completed product in containers; there’s no mess and no cleaning.
Lee continued “There’s no waste which is a cost saving of £80k per year which means the machine has paid for itself in just over a year – that’s a phenomenal ROI considering the life expectancy of this machine.”
Premier Foods, Knighton have also opted for the Premium Plus Service which guarantees response times of up to 4 hours. Minebea Intec Service Experts are available 14 hours per day to give exclusive technical support in resolving existing problems and assisting the staff. Lee concluded “I give Minebea Intec 10/10 and I’ve already recommended the X-ray machine to our other manufacturing sites at managers meetings. The product, the staff and the overall experience has been excellent.”
Mediacenter
类别 | 文件名称 | 语言 | 文件大小 | 文件类型 | ||
---|---|---|---|---|---|---|
Best Practices | ||||||
Best Practices | Best Practice // Food manufacturer saves £80k per year using Minebea Intec X-ray system | 英语 | 784 KB |